What are the most common casting methods?
The applications and processes of the most common casting methods.
There are many different casting processes.
It’s often incorrectly assumed that each casting process can achieve similar final castings in terms of quality, finish, function and complexity. Understanding the potential, as well as the limitations of each casting process is a vital first step in choosing the best manufacturing method for your part.
How many different casting processes are there?
There are over 10 different casting processes. The most common include:
- Sand casting
- Low pressure die casting
- High pressure die casting
- Gravity die casting
- Investment casting
What is sand casting?
The sand casting process involves pouring molten metal into a sand mould cavity, where it then cools and solidifies. After the metal has cooled, the mould is broken apart to remove the casting. Sand casting can produce complex net parts relatively quickly and cost efficiently compared to other processes. It's also a nearly 100% circular and extremely sustainable process with all the raw materials (sand and metal) being able to be reused.
What are the advantages of sand casting?
While sand casting is one of the oldest manufacturing methods, the process offers huge advantages for future production requirements; especially in areas such as electric vehicles with aluminium sand casting. As we globally push boundaries in technology, performance expectation and sustainability, prototyping becomes more and more essential. Sand casting can add huge value as a prototyping method.
Read more: How do you use DFM to design a high-integrity, precision sand casting?
Read more: How sand casting can help with rapid prototyping
Read more: How sand casting is contributing to a global carbon neutral future

What is investment casting?
A pattern is created from wax, which is then dipped into ceramic slurry. This is then heated and dried, creating a ceramic shell mould for casting. The wax flows out and the molten metal is poured into the cavity.
- Complex shapes can be created with investment casting, particularly in industries such as aerospace and automotive.
- Smaller features can also be made compared to sand casting, for example air cooling ducts inside a Tungsten turbine blade.
- Investment casting is mostly used for low production volumes.
What are low pressure and high pressure die casting?
Both are repetitive methods, but there are key process differences.
- Low pressure die casting introduces metal into the chill mould from below where gas pressure holds the metal in the die until it solidifies.
- High pressure die casting injects molten metal into a metal die under high pressure and high speed, allowing quicker casting production.
What are the other ways to make a part?
Machining from solid - Parts are machined from billets of metal into the required shape using CNC machines.
3D Printing - An additive process where parts are made layer-by[1]layer. There are 7 main types of 3D printing, including laser sintering (SLS) and fused deposition (FDM). A wide variety of materials can be used to help create complex shapes, but it' s slower and more costly for all but one-offs.
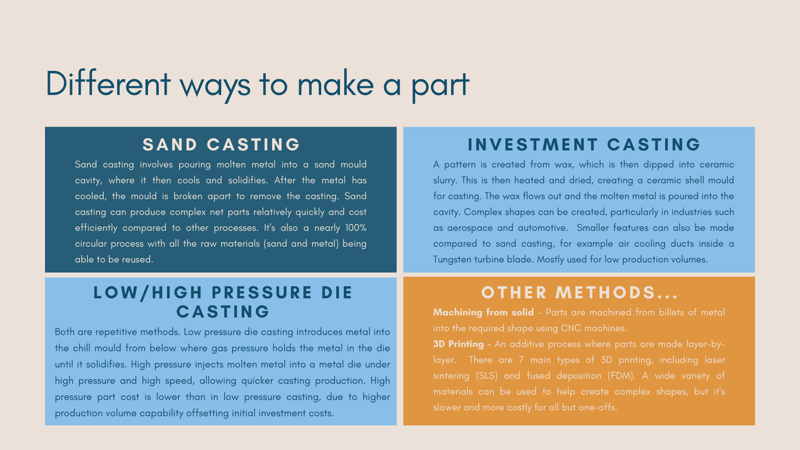