What are the aspects of a good sand casting design?
An overview of the DFM process and the considerations for good sand casting design.
What does good quality sand casting design look like?
Good casting design will optimise areas such as draft angles, split line placement, wall thinness and junctions in the part. This ensures design functionality is maintained while meeting specified material properties such as hardness, durability and ductility. Although it doesn't appear in the final part, the design of the runner and feeder system is critical too.
How can you optimise for part design and function with Design for Manufacture (DFM)?
Working with your sand casting supplier at the (Design for Manufacture) DFM stage will help to identify ways to optimise the part design function, process used and material selection to achieve the desired properties for your casting and project goals.
How can you model to achieve a high-integrity sand casting?
Effective modelling is an important part of the sand casting DFM design process. It can predict material properties and residual stresses that may impact part function- essential for material integrity and casting quality.
- CAD software creates the 3D model and 2D drawings required to make it.
- Magma is a simulation package which models the flow and solidification of the metal, aiding the placement of chills and feeders to allow the engineer to maintain control of the solidification process. This minimises misruns and helps achieve the correct material properties (for example strength and hardness) in the finished part.
- Arena Flow simulates how the sand flows into a mould for blowing a core with a core blower.
How can you maximise the DFM process for your sand casting project?
Start at the end.
It’s important to know exactly what you’re trying to create with your cast part, and start with the end in mind. For example, are you creating a MLP (Make Like Production) prototype to match production quality (with associated dimensional accuracy and replicated production properties)? Or do you just need a prototype of a shape quickly for testing purposes?
The answer may influence your design considerations as well as the best sand casting process methods to optimise part function and properties. Some prototypes won’t require methods that closely match production and final casting properties, whereas others will have to consider these much more carefully.
Can I change the part design part way through the production process?
The various elements involved in aluminium sand casting have complex interdependencies, and accommodating design changes is a strength of the sand casting process (soft tools are easily modifiable and printed cores allow for quick changes). ]
If the design is changed, the process can be altered with new simulation and different runner feeder systems and chill placements.
What are the other ways to make a part?
Machining from solid - Parts are machined from billets of metal into the required shape using CNC machines.
3D Printing - An additive process where parts are made layer-by[1]layer. There are 7 main types of 3D printing, including laser sintering (SLS) and fused deposition (FDM). A wide variety of materials can be used to help create complex shapes, but it' s slower and more costly for all but one-offs.
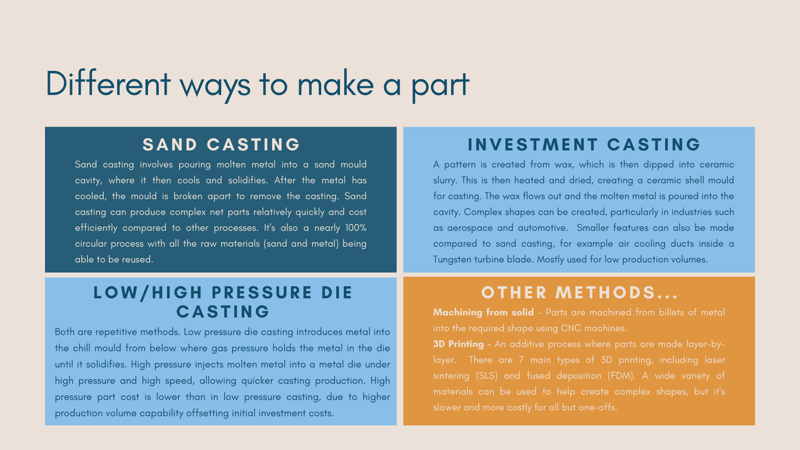