Innovating at the casting edge.
We are the global leaders in complex metal shape casting technology.
Masters of metal since 1946
Good casting practice lies in complex science, metallurgical and chemical interactions, thermo and fluid dynamics, stresses and strains.

COMPLEX CASTING INNOVATION
With the largest independent foundry in the world, our engineers have been designing, manufacturing, and verifying complex precision sand castings for over 70 years. With a diverse range of product dimensions and an abundance of applications, our process involves the harmonisation of engineering and mathematical iteration to ensure a timely solution is delivered for every customer.
Our desire to innovate and improve the casting process for the future never dulls. While the challenge to be leaner, greener, and meaner increases each year, we’re committed to meeting these demands by pushing the boundaries of what is possible to produce high-quality castings that are lighter, more powerful, and more reliable.
To find out more about the sand casting process and the technology we use, click here.
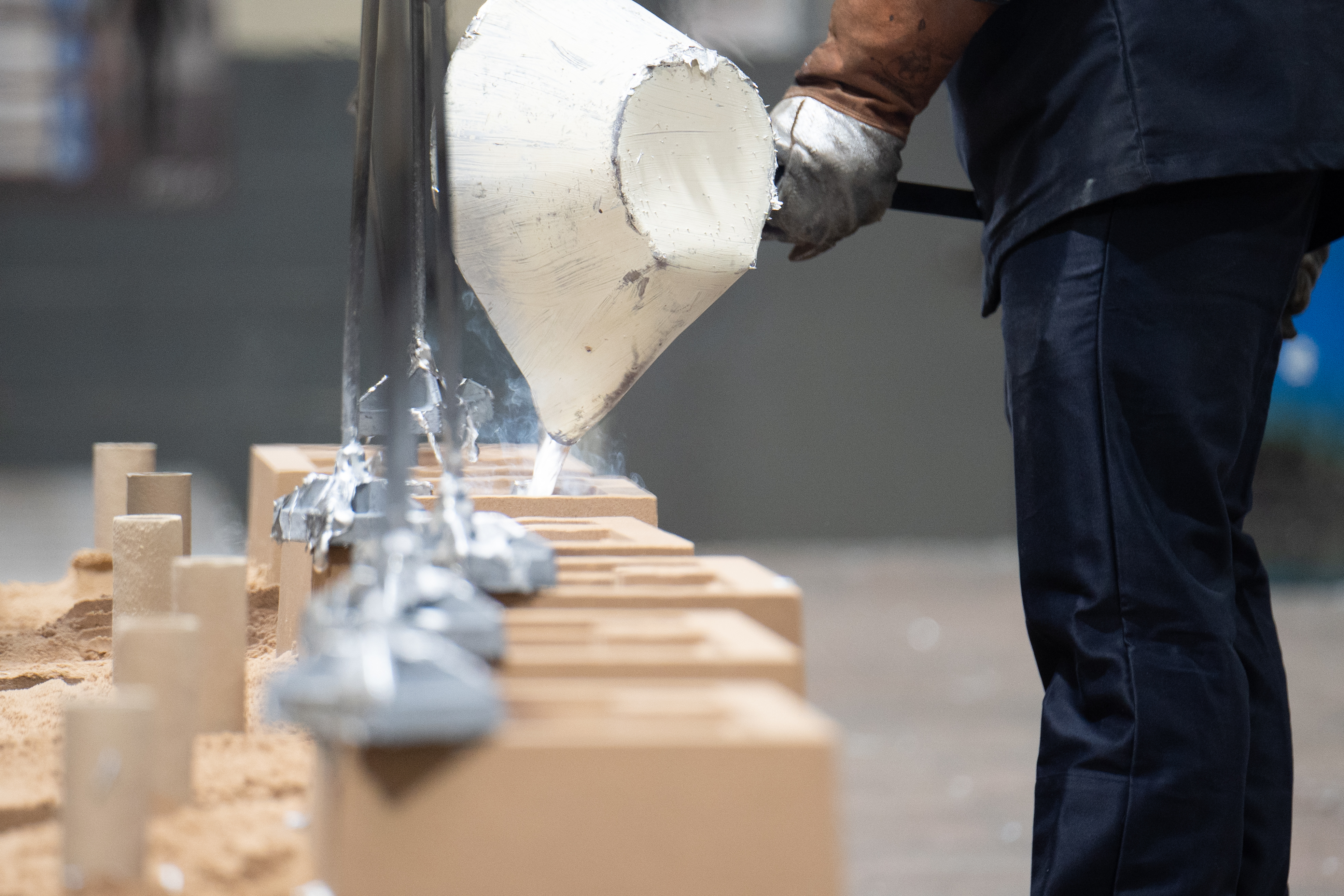
At Our Specialized Prototype Aluminium Foundry, We Take A Fresh Approach To Meeting Product Development Demands By Providing Pre-production And Production Intent Prototypes. Our High Precision Sand Castings Cater To A Range Of Markets, Including Engine, Vehicle, Aerospace And Industrial, With A Focus On Adding Value And Maintaining Integrity Throughout The Entire Process.
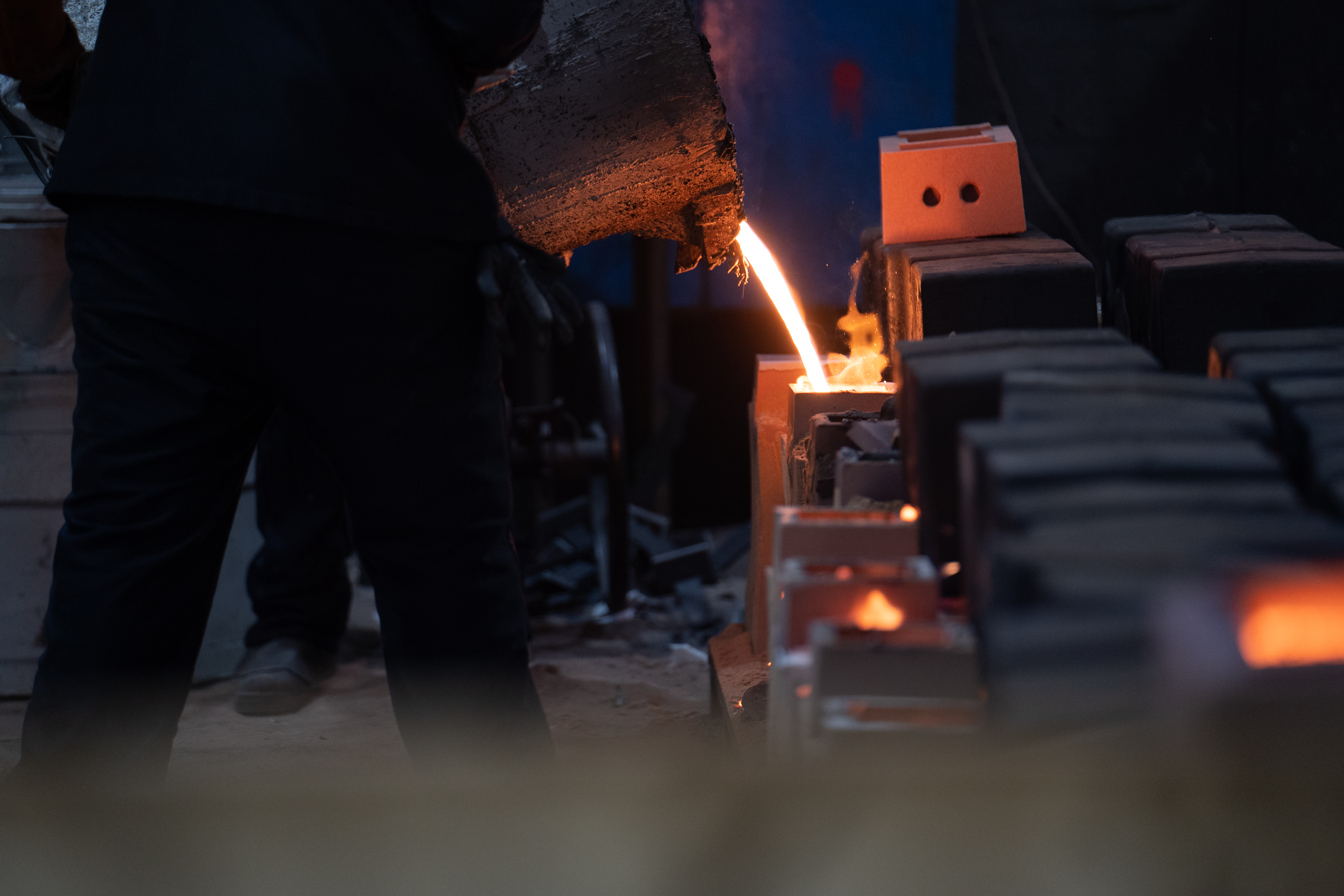
With Our Diverse Range Of Materials, Including Grey Iron, Ductile Iron, Compacted Graphite Iron, Steel, Nirisist, And Adi, Our Foundry Is Capable Of Casting Weights Ranging From 1kg To 500kg. Our Approach To Prototyping Is Always With An Open Mind, Seeking Ways To Add Value And Ensure Highly-integrity Castings Are Delivered Successfully.
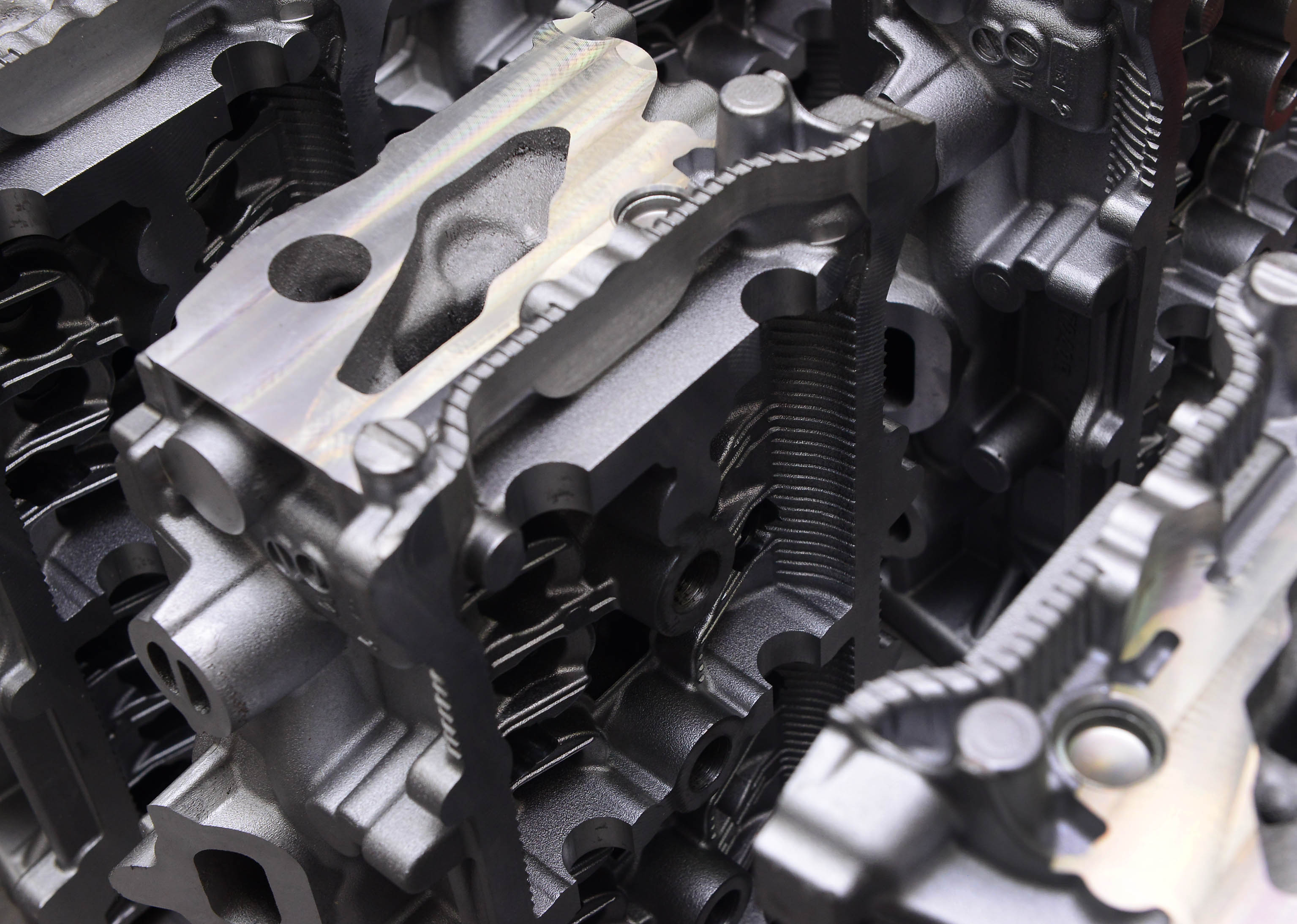
Experience The Best Of Both Worlds With Our Series Foundries. Utilising The Precision Sand Cast Process, We Offer Flexibility While Also Optimising Economies Of Scale For Limited And Pre-production Tier 1 Automotive Supply. From Engine Cylinder Blocks To Ancillaries, We Provide Top-quality Castings To Meet All Your Needs.
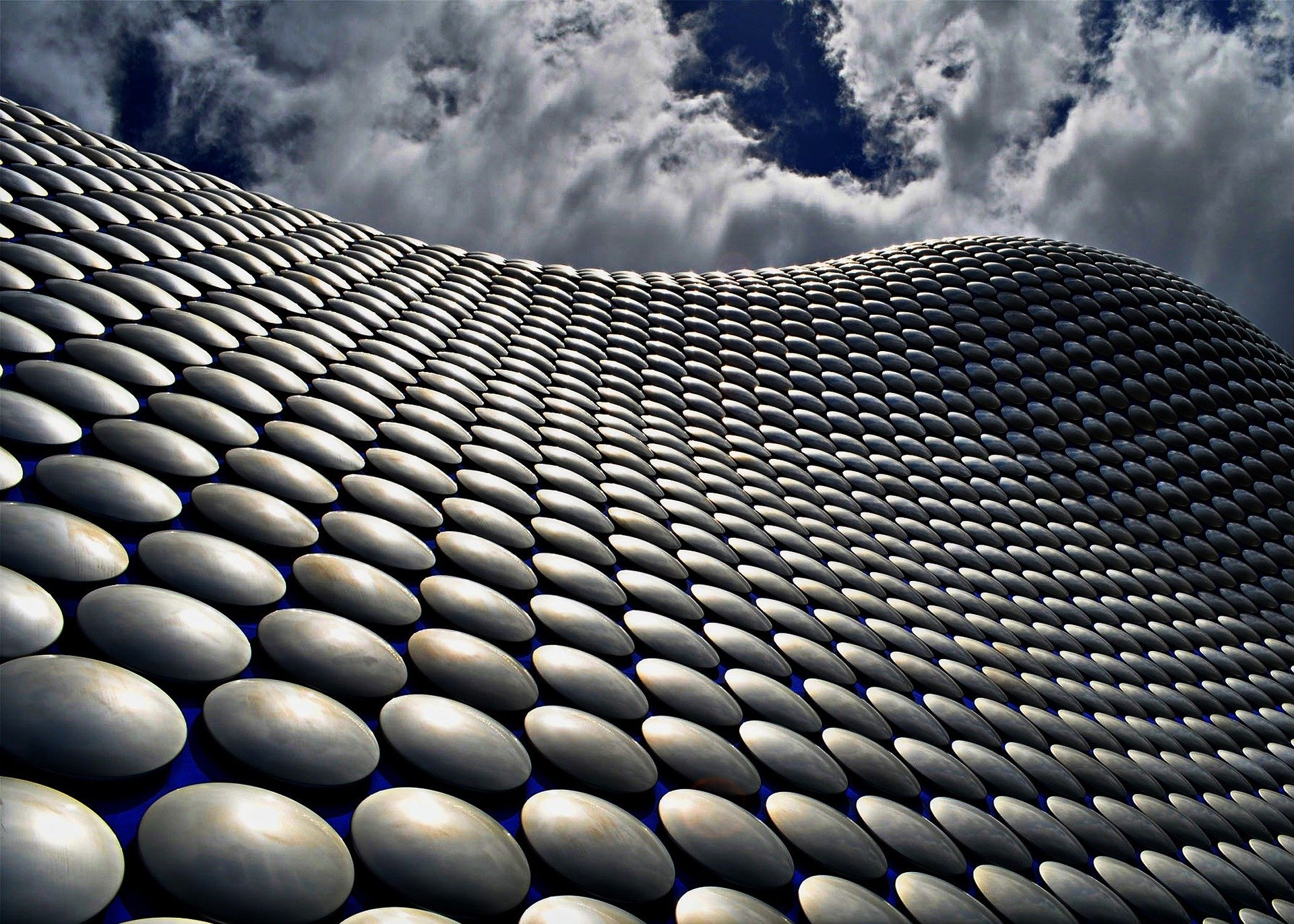
Our State-of-the-art Facility Allows Us To Seamlessly Integrate Automated Casting Processes, Enabling Us To Produce An Extensive Range Of Top-notch, Intricate Aluminium Castings That Are Both Sizeable And Complex.
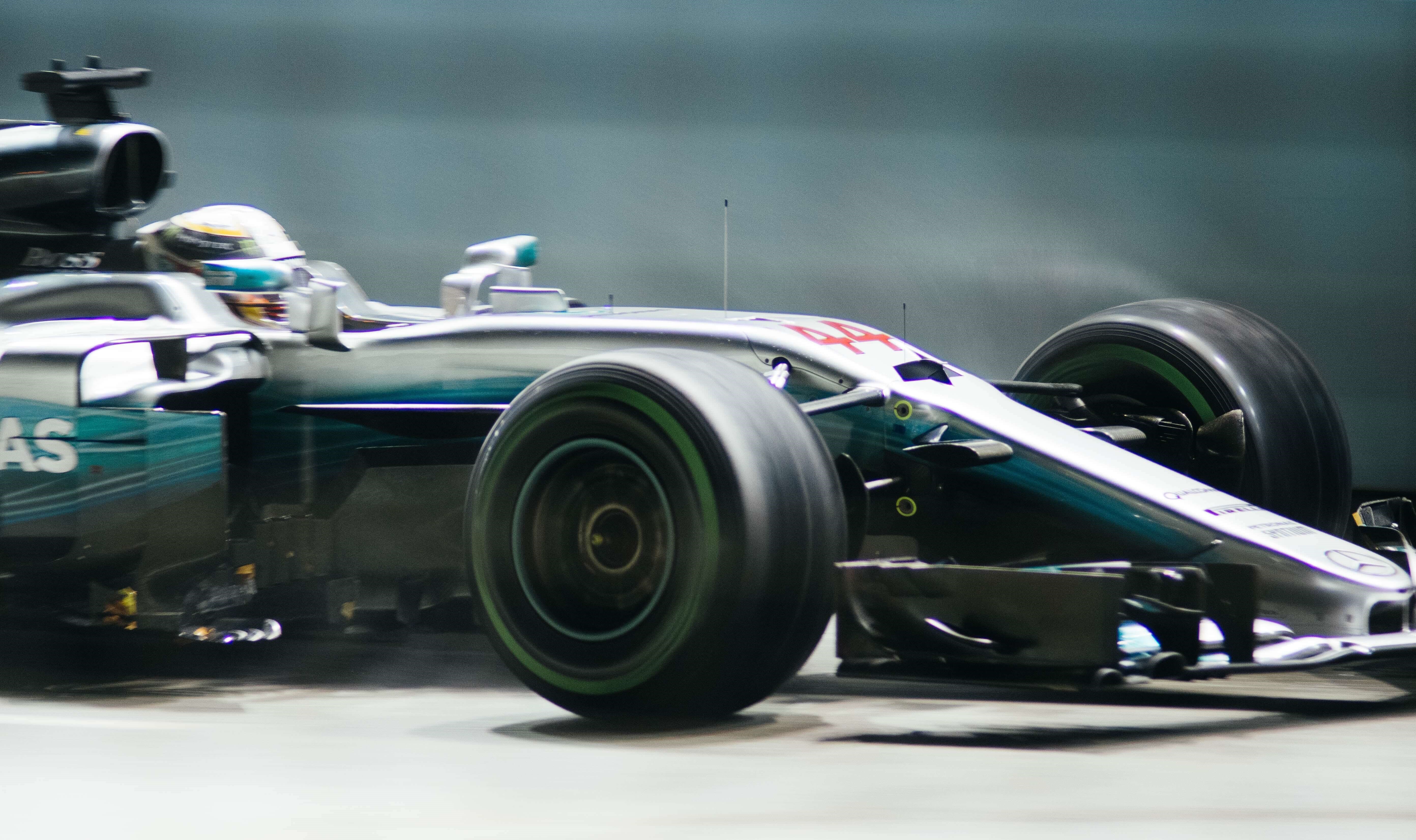
Our specialist prototype aluminium foundry meets product development demands with a novel approach- for both pre-production and production intent prototypes. Whether you need high precision sand castings for engine, vehicle, aerospace or industrial markets, we add value and integrity at every stage of the process.
HIGHLY COMPLEX AIR SET SAND CASTINGS
Our core capability focuses on highly complex air set sand castings. We’ve developed an extensive library of alternative aluminium alloys for the diverse applications demanded by our varied customers.
Our Aluminium Cast products demonstrate superior quality and performance through application of best practise and technology. Multiple sand medias Silica, Chromite, Alumina, Zircon are employed along with appropriate coatings and chill placement within our high precision engineered moulds.


INNOVATIVE ALUMINIUM CASTINGS FOR THE NEXT TECHNOLOGICAL GENERATION
The key driver for our prototype aluminium casting has been technological and legislative advances in vehicle and engine design.
Low Carbon vehicle technologies need lighter, stronger and more powerful engines – and the same demands are true of the castings. At Grainger & Worrall, we’ve led an innovative and exceptional process to design, make and verify exceptional prototype castings, allowing us to meet the demands of the next generation.
Our series foundries employ the flexibility of the precision sand cast process whilst also optimising economies of scale for the limited and pre-production Tier 1 automotive supply. This includes engine cylinder block, cylinder head castings and ancillaries.
HIGH INTEGRITY, PRECISION AUTOMOTIVE CASTINGS
The consistent repeatability of high integrity automotive castings is supported across annual Volumes of 1,000 – 10,000 units, with an overall facility volume of 90,000 moulds per annum. Typical projects undertaken by our aluminium foundry support the high casting mechanical integrity and cosmetic quality requirements of the luxury vehicle and sports-car market.
We also process cast components further, inclusive of machining, validation, sub-assembly or final assembly to customer requirements. This means we provide a total solution, including validated components ready for engine or vehicle build.

Our bespoke facility gives us important flexibility when it comes to the automated casting process, and we use this to supply a variety of high quality, large and complex aluminium castings.
REPEATABILITY AND INTEGRITY OF MANUFACTURE
Repeatability and high confidence in the manufacture of moulds in low to medium volumes has resulted in the successful delivery of multiple projects from two metre long automotive torque tubes, commercial transmission housings through to three dimensional sand-cast aluminium panels.

A CREATIVE, FUNCTIONAL AND SUSTAINABLE FOUNDRY
We created the foundry specifically to be creative yet functional, driven by customer requirements. This allows a combination of flexibility and low tooling cost to support varied requests for high quality niche casting supply. The foundry includes articulated mixers, fill and strip stations and low-level knockout systems.
Thermally stable castings with fine surface detail can be produced in a variety of aluminium alloys suitable for:
• Large transmission and architectural applications such as cast aluminium wall panels and roof tiles creating impressive building facades for prestige building projects.
All sand is thermally reclaimed in house supporting a sustainable and cost effective supply solution.
We have a co-operative understanding of our Motorsport customers, including unique confidentiality, high integrity casting and tooling requirements. At our foundry in Bridgnorth, we’ve incorporated a specific process that’s been designed and developed to produce Formula One grade castings in support of the Motorsport Industry.
UNRIVALED EXPERIENCE IN POWERTRAIN AND TRANSMISSION PROGRAMS
Our experience in racing, rally engine and transmission programs is unparalleled. We use this experience to meet demanding requirements for high complexity, high quality and compressed lead-times place, as well as technology to achieve the highest level of casting quality in both Aluminium and CGI (compacted graphite iron).
CHAMPIONSHIP WINNING ENGINE PROGRAMS
We’re unique in the provision of a team and facility dedicated to Motorsport providing quality assured components.
In house computer tomography and casting simulation technology combined with the Cosworth Casting process consistently provides the race engine designer with the tools required to deliver multiple championship winning engine programs.
Over many years, we’ve developed the roll-over casting process to meet the latest requirements in high integrity castings. As a result, we produce the most reliable castings in the world.
Only defect free parts get delivered to our customers. These castings are achieving higher strengths and levels of durability whilst meeting the needs of engine downsizing; meeting the key challenges of being lighter, thinner and more accurate.
MAKING GLOBALLY RENOWNED, RELIABLE CASTINGS

THERE ARE GOLDEN RULES THAT EXIST FOR MAKING ‘THE PERFECT CASTING’.
- Developed over recent years by many academics these focus on the avoidance of defects borne out of shortcomings in liquid melting, effects of oxide (bifilm) formation through turbulent pouring and gas bubble generation, importance of temperature gradient and adequate feeding.
- There are others but so far these ‘ideals’ can be summarised as the Casting Process. We operate a specialised industry leading Low Pressure Pumped system, formally known as Cosworth Rollover Casting Process.