Grainger & Worrall is a global leader in sand casting complex metal shapes. We support projects from
design consultancy, tool design and manufacture to prototype casting, finishing, machining, and
assembly.
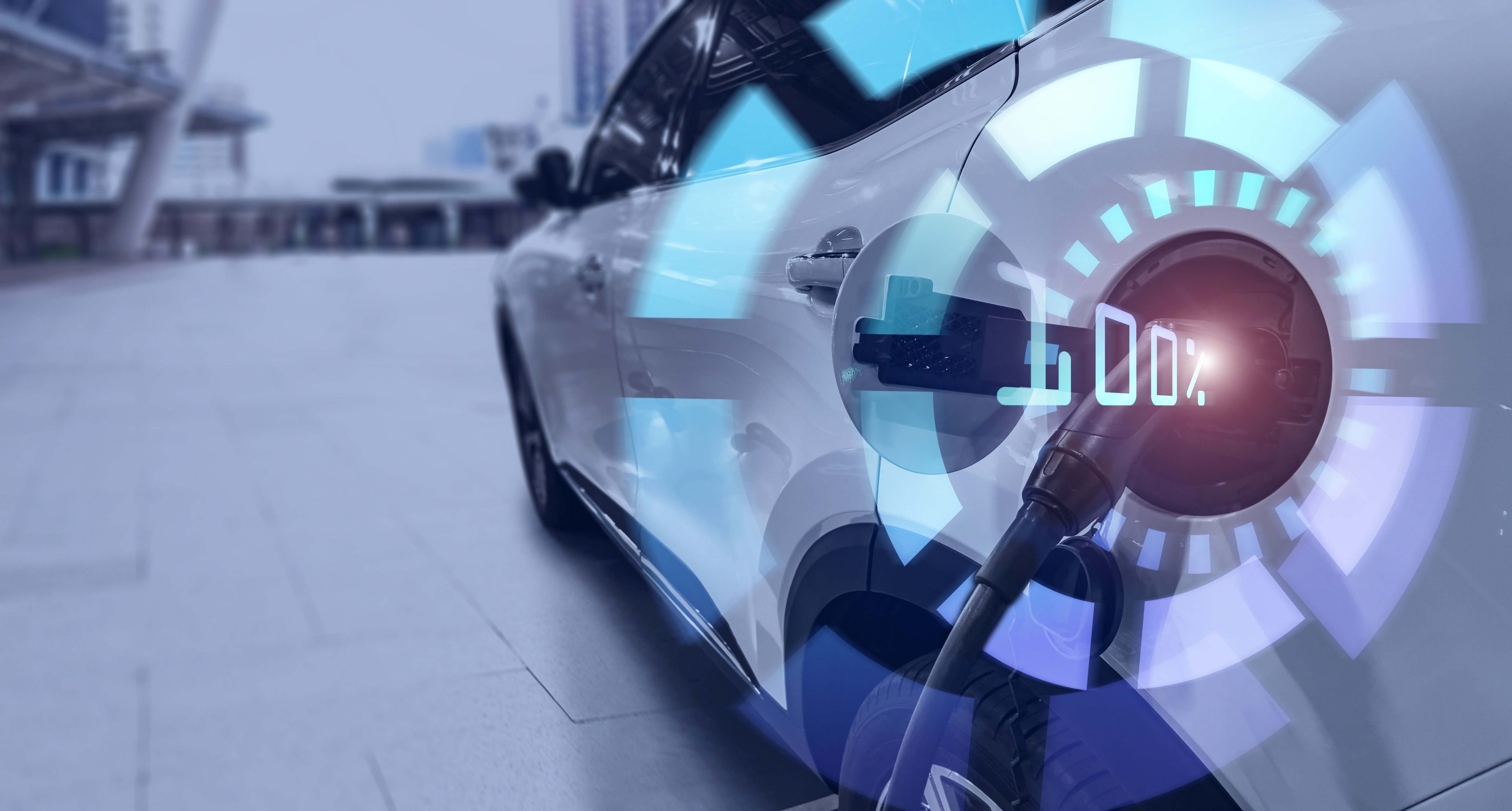
Grainger & Worrall specializes in producing lightweight, high-integrity sand castings made of aluminium that meet the automotive industry's demands for Internal Combustion Engine (ICE) components. Our sand casting expertise, combined with our in-depth knowledge of materials, allows us to create customized aluminium alloys that are strong, precise, and lightweight, thus enabling the development of modern ICE components and applications. Our accurate and rapid production process ensures consistent quality every time.
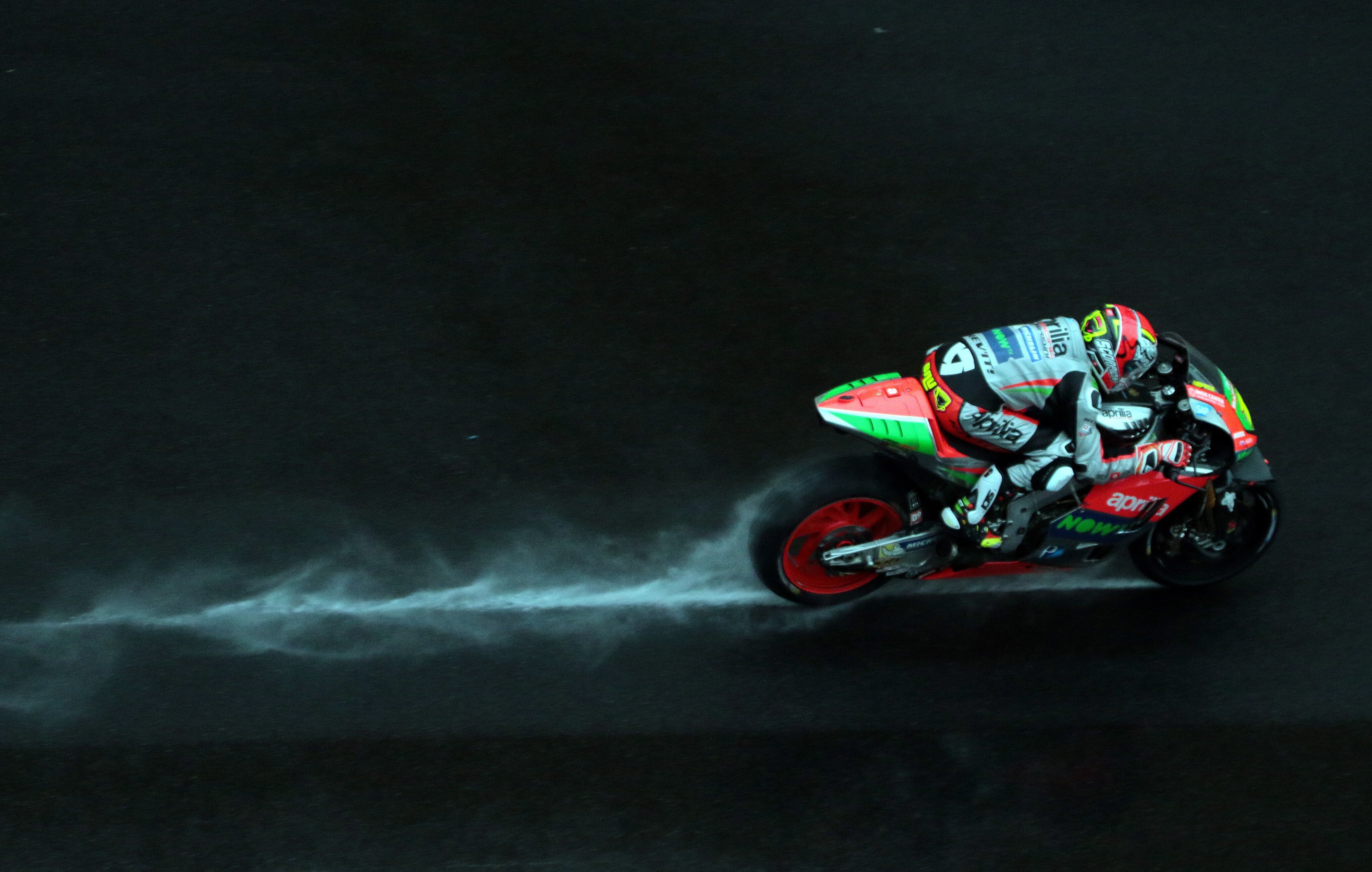
Here at Grainger & Worrall, we know motorsport. Perhaps even more importantly, we know our motorsport customers. This includes your need for confidentiality, high-integrity, precision castings and compressed lead times.
We've developed a specific casting process to produce the Formula One grade castings demanded by the motorsport industry. This allows us to produce the most reliable, defect-free castings in the world.
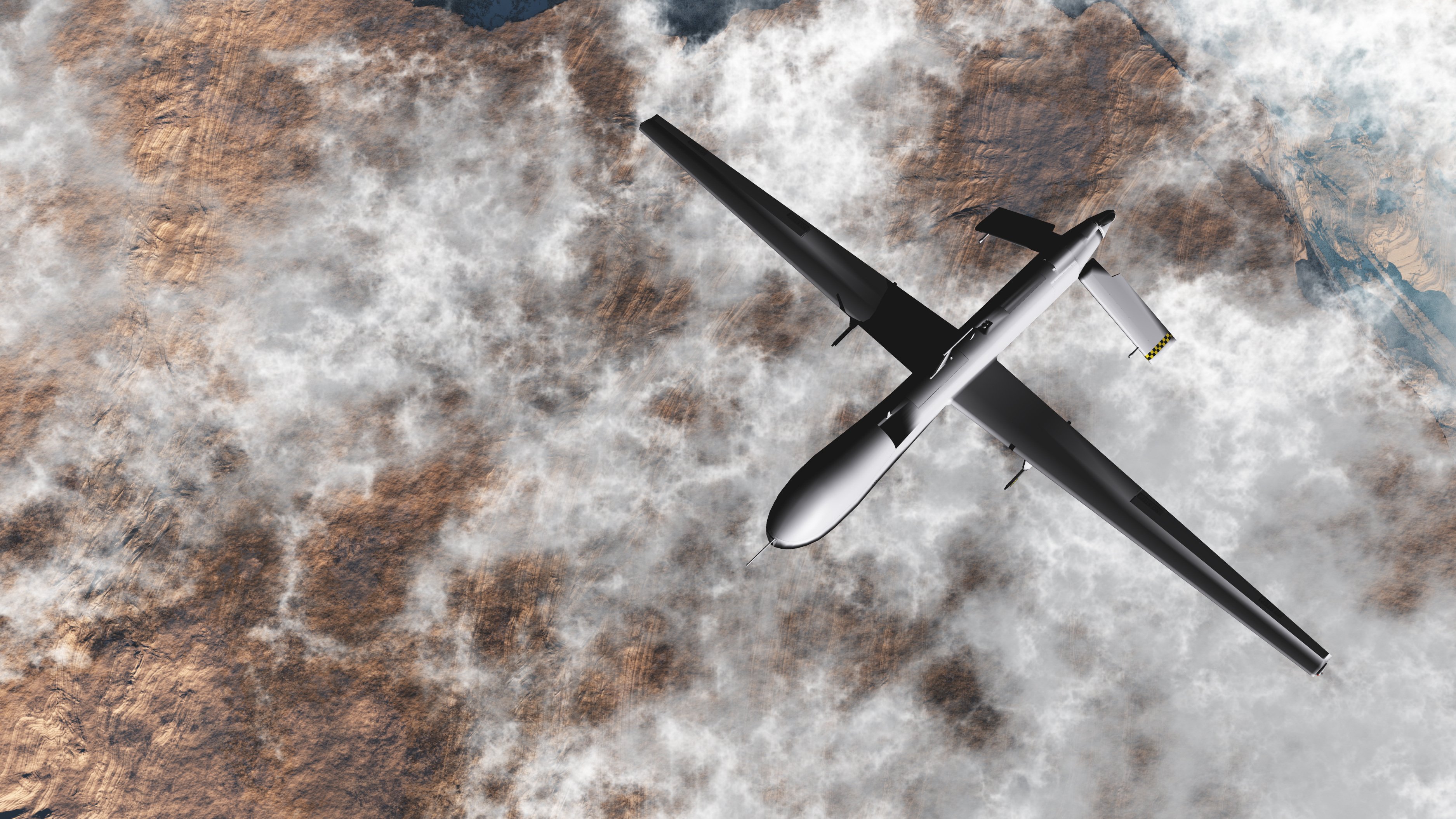
We create the high-precision, powerful and lightweight castings required in by the aviation industry. This includes properties of fatigue resistance, high surface finish and dimensional stability.
Aluminium sand castings and bespoke alloys allow us to create the lightweight, complex and strong metal shapes required for powerful aviation performance while reducing aerodynamic drag. This includes engine components for single and twin engined aircraft, as well as helicopters.
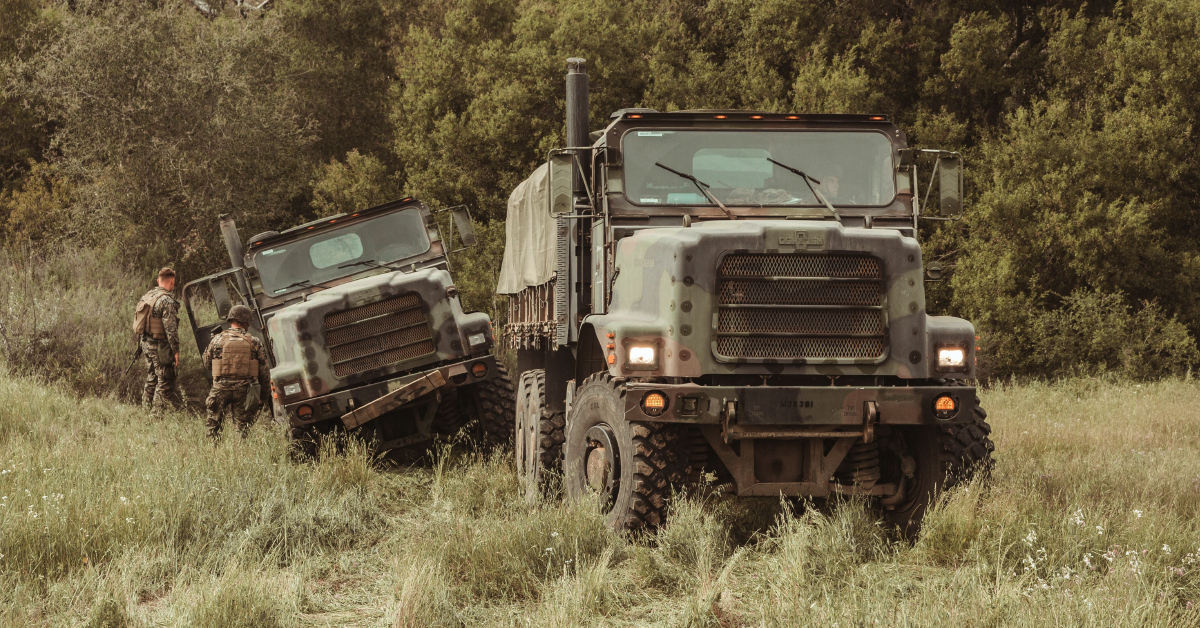
Defence procurement requires R&D innovation, production flexibility and expert engineering. Our sand casting experience allows us to work with your engineering or technical directors to meet your defence programme requirements with a precision-driven, right-first-time approach.
We understand the dynamics of defence, and our capacity allows us to respond to changes in timescales. We specialise in innovating from concept through to production. And we do it fast.
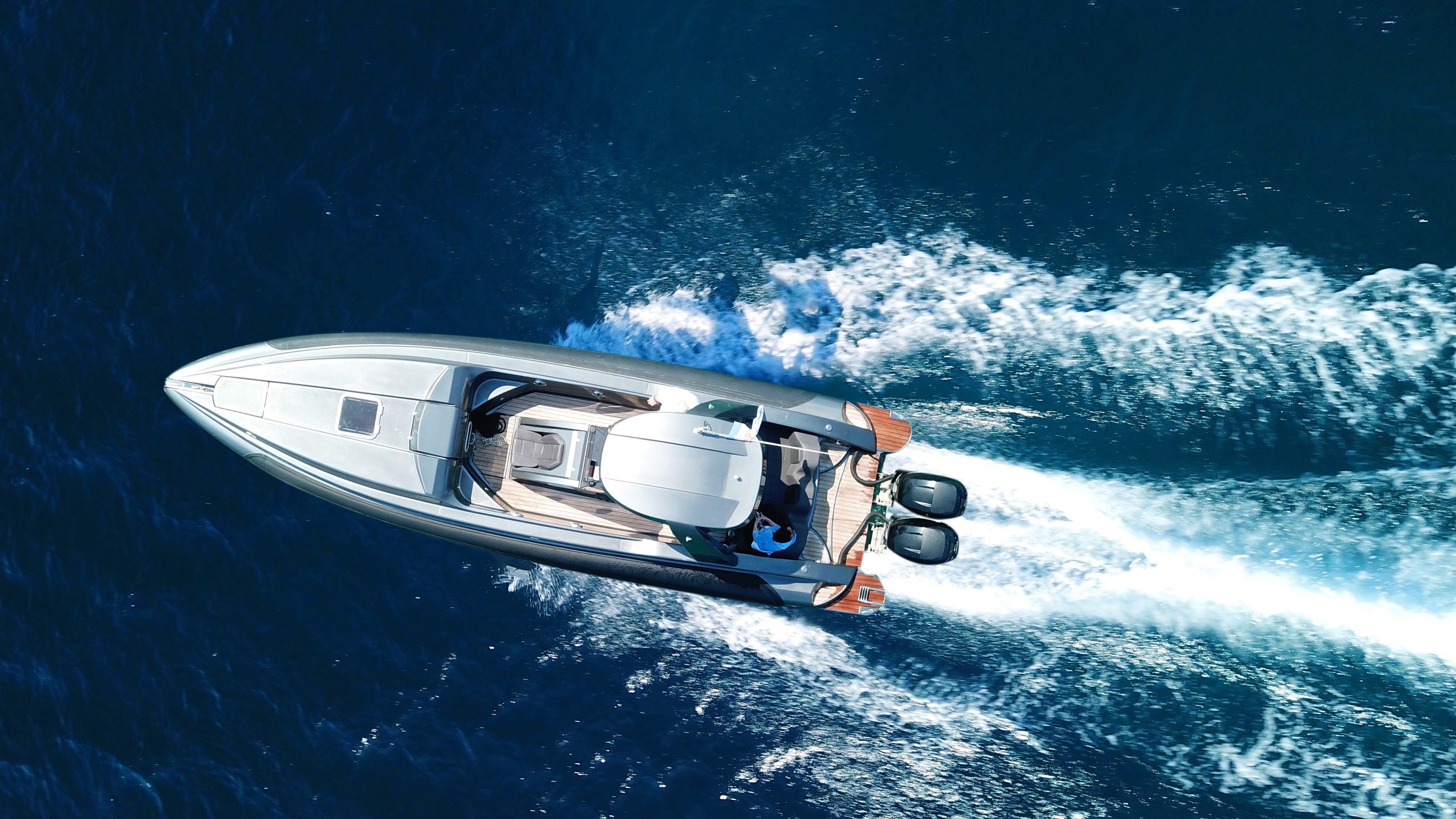
We create the complex metal shapes required in marine-grade castings. Our materials knowledge allows us to create castings in marine-grade aluminium alloys, optimised for performance, function and properties such as machinability, erosion and corrosion resistance.
We combine our sand casting expertise with cutting edge technology to meet your high performance requirements. And we do it fast, without jeopardising quality control or casting accuracy.
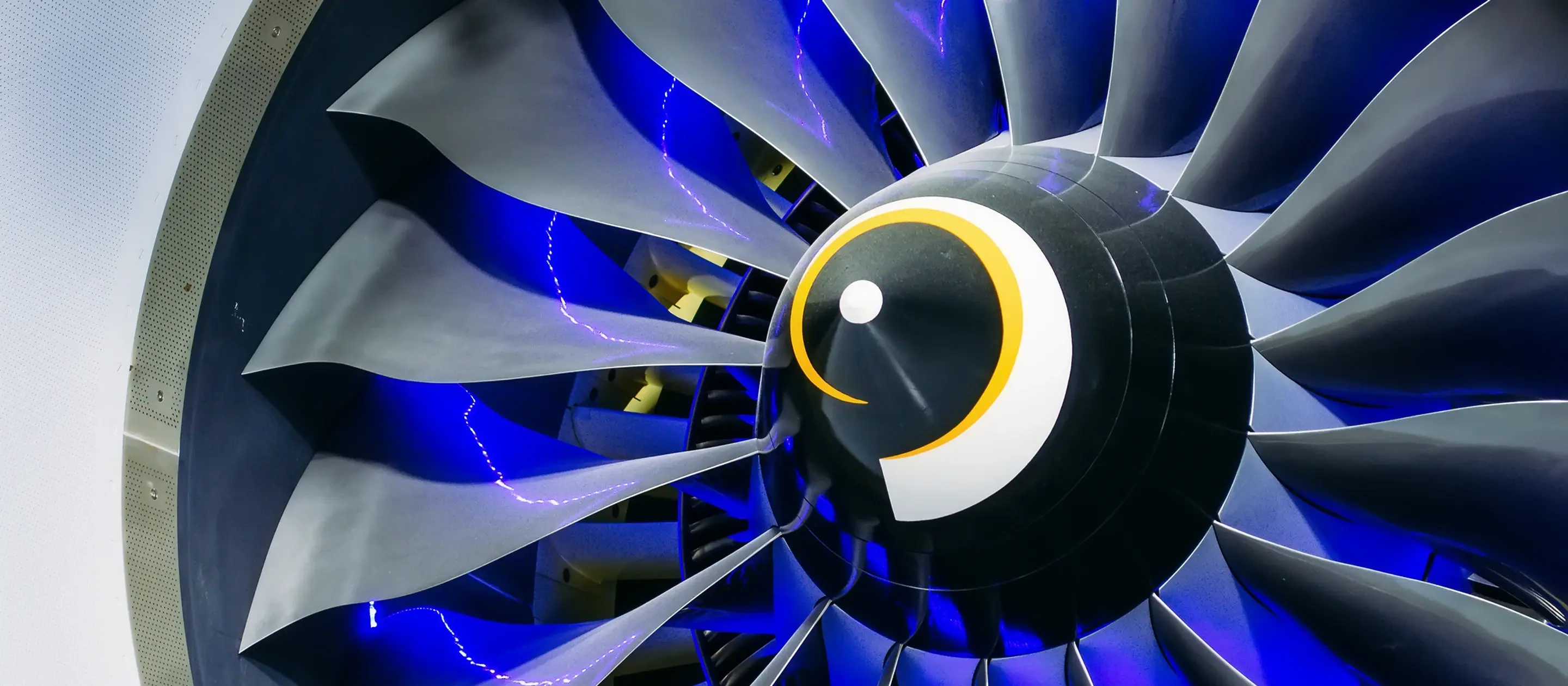
Our materials knowledge and innovative prototyping approach allow us to produce sand castings that meet the engineering challenges faced by the energy sector against a global background of achieving a carbon neutral future.
Aluminium castings allow us to create the lightweight, durable, wear resistant and dimensionally stable metal shapes required to both help reduce emissions and meet the exacting energy sector performance demands.
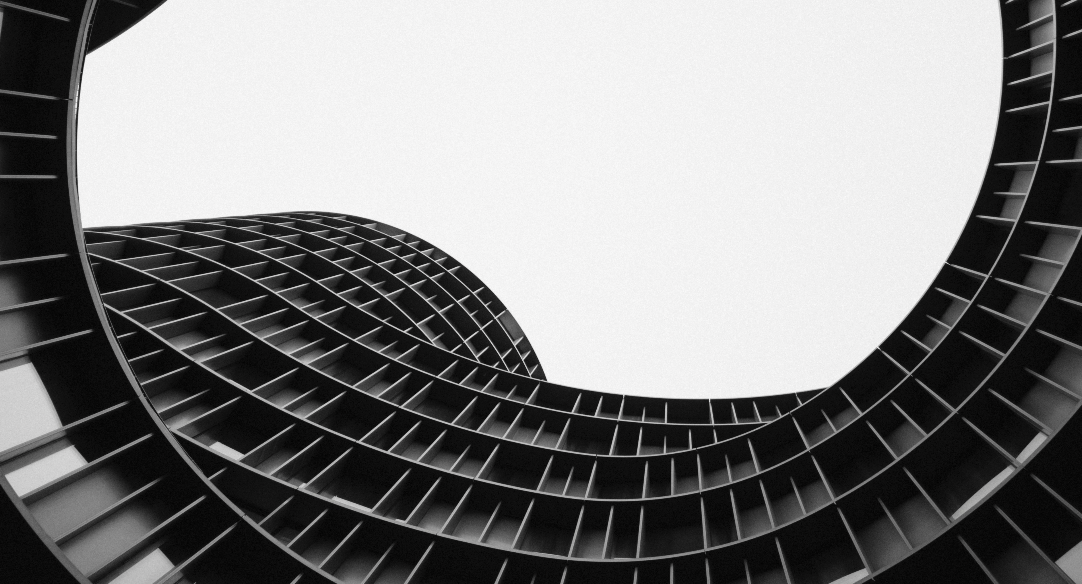
We approach architectural sand casting challenges with creativity and flexibility, producing durable castings that are often large, niche and highly technical. Our processes give repeatability and manufacturing confidence in low and medium volumes needed for architectural castings
Aluminium castings allow us to create the lightweight, complex yet strong metal shapes required in architectural projects such as prestige facades, roof panels and tiles.
Future Shape Technology.

+0
Successful projects
+0
Customers
+0
Countries
Grainger & Worrall have been at the cutting edge of casting technology for over seventy years. As regulatory changes have driven technological innovation, we have helped world-class motorsport and automotive companies (ICE and EV) move with the times.
Engineering
-
Casting Simulation
In the past the traditional approach to casting development was by largely trial and error. This would involve producing a casting gating system by a foundry engineer’s best estimate, then if this failed, a second, third etc version would be produced until a satisfactory casting was achieved.
-
Rapid Prototyping
We apply many approaches to rapid prototyping depending on the product production
requirements. Sometimes a hybridised rapid prototype is best, sometimes full rapid
prototyping is best, our experience in this complex field will add value to your program. Read more... -
Tooling Design and Patternmaking
Tool making is a core competency of Grainger & Worrall and we are one of few foundries to
resource and manage this entire activity in house. Both our pattern making facility and design capability is continually expanding to support our customers demand for directly milled high quality resin patterns and tooling up to fully automated production core-box rigs.
Castings
-
Giga Casting
Revolutionise the automotive industry with giga casting, the game-changing process that allows manufacturers to cast massive, load-bearing parts in one seamless piece. This breakthrough technique empowers engineers to design leaner, meaner vehicles with reduced components, streamlining the supply chain and delivering unparalleled efficiency.
Find out more here.
-
Automated and Low-pressure casting
We have two automated continuous melting facilities with the capability of producing
over 3,500 high integrity parts per week.
With consistency in the metal preparation and delivery, this enables us to scale up to
achieve high precision and integrity castings for Niche volume supply. -
Prototype Foundry
Casting a wide range of Aluminium Alloys for both pre-production and production intent prototypes.
Grainger & Worrall’s specialist prototype aluminium foundry approaches product development with a novel approach adding value, delivering successful high integrity precision sand castings for engine, vehicle, aerospace and industrial markets.
Machining
-
Precision Machining
Our unique position in the market place has provided both insight and experience into the delivery of quality assured complex precision machined components across the automotive, aerospace and affiliated sectors.
-
Cylinder Head & Engine Block
Grainger & Worrall Machining has developed a capability to machine high feature content Cylinder Heads and Engine Blocks without using traditional Horizontal techniques. Whilst our Horizontal approach offers cycle time advantages in the production environment, it also presents some disadvantages in the small batch and prototype environment.
-
Procurement Outsourcing
Grainger & Worrall managed procurement outsourcing provides second tier supplier management and quality assured machining services in support of its high quality castings. Typically this reduces product development costs and allows our customers to focus on the overall product rather than managing additional subcontract service providers.
Giga casting
Giga castings take a fundamentally different design and manufacturing approach to traditional vehicle manufacturing, casting front and rear pieces in a single piece.
Giga casting is driving a revolution in automotive manufacturing. The process can produce large structural castings in a single net piece, reducing production and assembly time, as well as cost. Giga casting also has wider implications for transforming manufacturing across industries.
The giga casting process allows large structures to be cast in single pieces, reducing the need for welding. Aluminium alloys and new casting components used in giga casting contribute to increasing lightweighting further.
Benefits of the giga casting process include the ability to cast large structures, reduced lead times and faster assemblies. Casting single pieces, rather than requiring hundreds of parts also significantly reduces manufacturing costs.
DRIVING A GREEN AGENDA.
Grainger & Worrall are committed to driving a sustainable operating model and continuing to develop our green agenda. We do this through focusing on the key areas of energy, environment, technology and lightweighting.
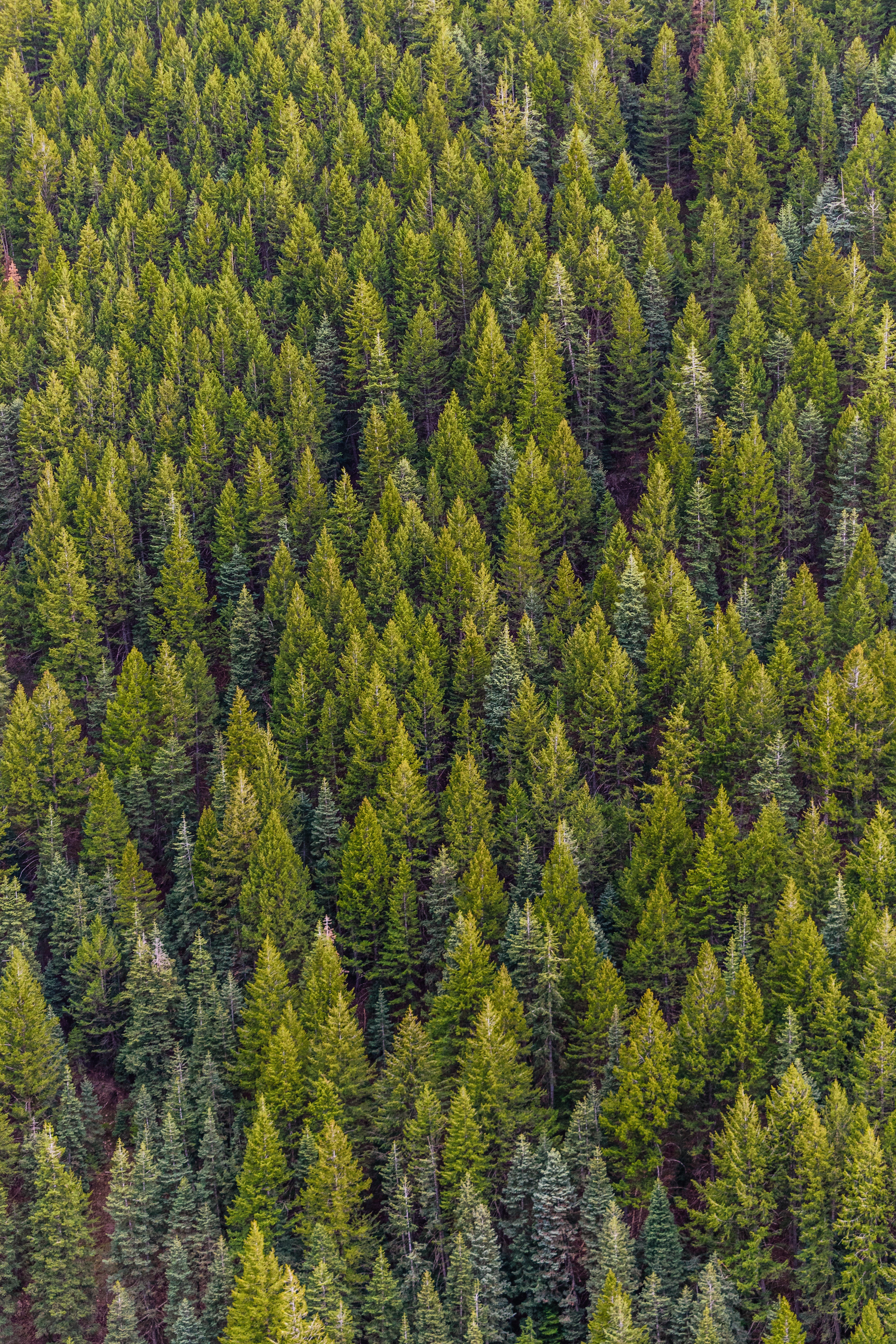