Engineering the future.
We are the global leaders in complex metal shape casting Engineering.
Designing Castings since 1946
The DFM process is fully embraced and our engineering resource is available to support you in the design and feasibility of aluminium or ferrous alloy castings.

Engineering innovation
A typical project often includes production intent design support, DFM and new product launch. By combining industry knowledge and the latest computer-based technologies, our team are able to provide foundry process analysis, review and rectification services during the production phase.
Our knowledge of Aluminium alloys material science has enabled us to develop unique alloys to employ in "make like production" scenarios. This enables us to make Aluminium prototype castings that behave like production parts. Likewise with iron castings, we can use our database of ferrous alloys to tailor material properties to suit your application.
As industry leaders, our ability to innovate comes about by engaging the talents of other industry experts, universities and like-minded customers who help us develop new processes and ensure we’re always at the cutting edge of casting engineering.
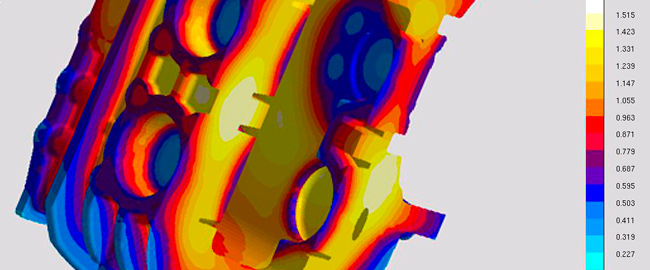
Gone Are The Days Of Trial And Error In Casting Development. In The Past, Foundry Engineers Would Produce Multiple Versions Of A Casting Gating System Until A Satisfactory Result Was Achieved, Leading To Wasted Time, Money, And Lengthy Lead Times For Costly Parts. But With The Advent Of Casting Simulation And Magma, The Process Has Become More Efficient, Precise, And Cost-effective. Say Goodbye To The Old Ways And Embrace The New Era Of Casting Development.
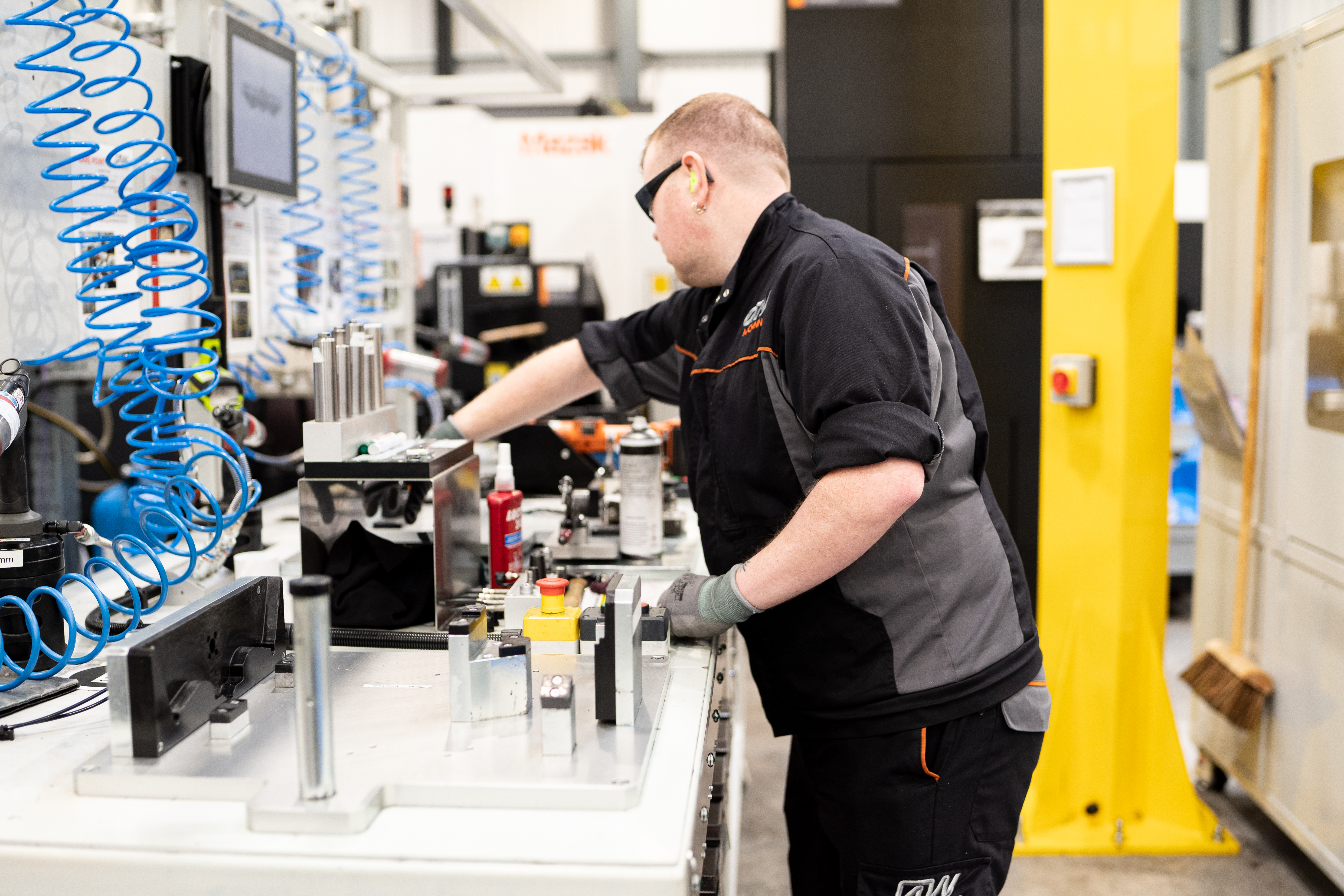
We Take Pride In Managing Our Tool Making Process Completely In-house, Setting Us Apart From Other Foundries. Our State-of-the-art Facility Is Both Secure And Confidential, Allowing Us To Provide Exceptional Service And Technical Excellence. With Over 60 Years Of Experience In Pattern And Tooling Manufacturing, We Have Earned An Enviable Reputation In The Industry For Delivering High-quality Products.
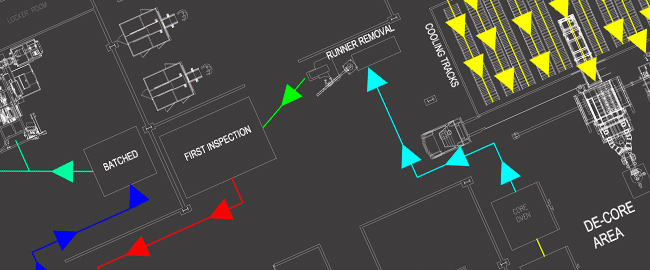
For Our Foundry Process Consultancy, We've Brought Together A Team Of Experts In Tooling And Casting Prototype Manufacturing, Simulation Techniques, Project Management, Product Launch, And Manufacturing Process Development. This Comprehensive Range Of Skills Enables Us To Offer Our Customers A Complete "design To Production" Solution.
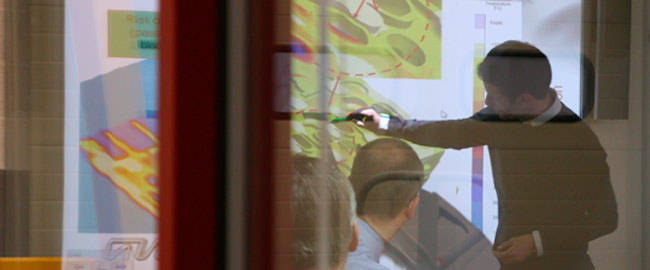
Our Team Understands The Challenges Of A Constantly Evolving Marketplace. That's Why We've Created A Customised Project Management System That Can Handle Any Project, No Matter The Size Or Complexity. With Our System, You Can Rest Assured That Your Project Is In Good Hands.
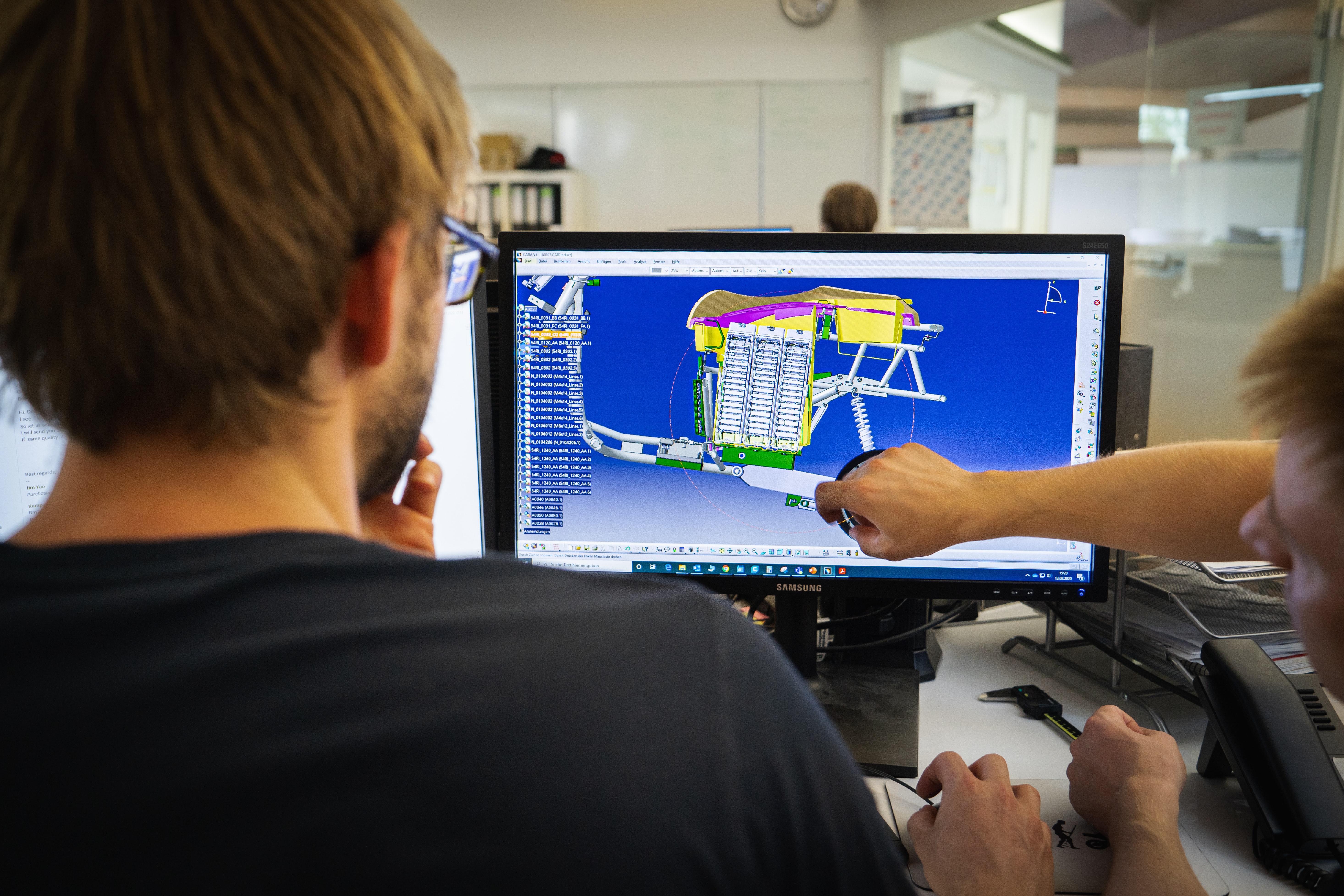
Our Cutting-edge Facility Empowers Us To Create And Implement An All-encompassing Strategy To Mitigate Casting Risks And Ensure Timely And Cost-effective Project Delivery. Our Unwavering Focus On Quality Is Anchored By A Rigorous Npi Process, Bolstered By A Resilient Business Foundation And Backed By Easily Accessible Managed Resources.
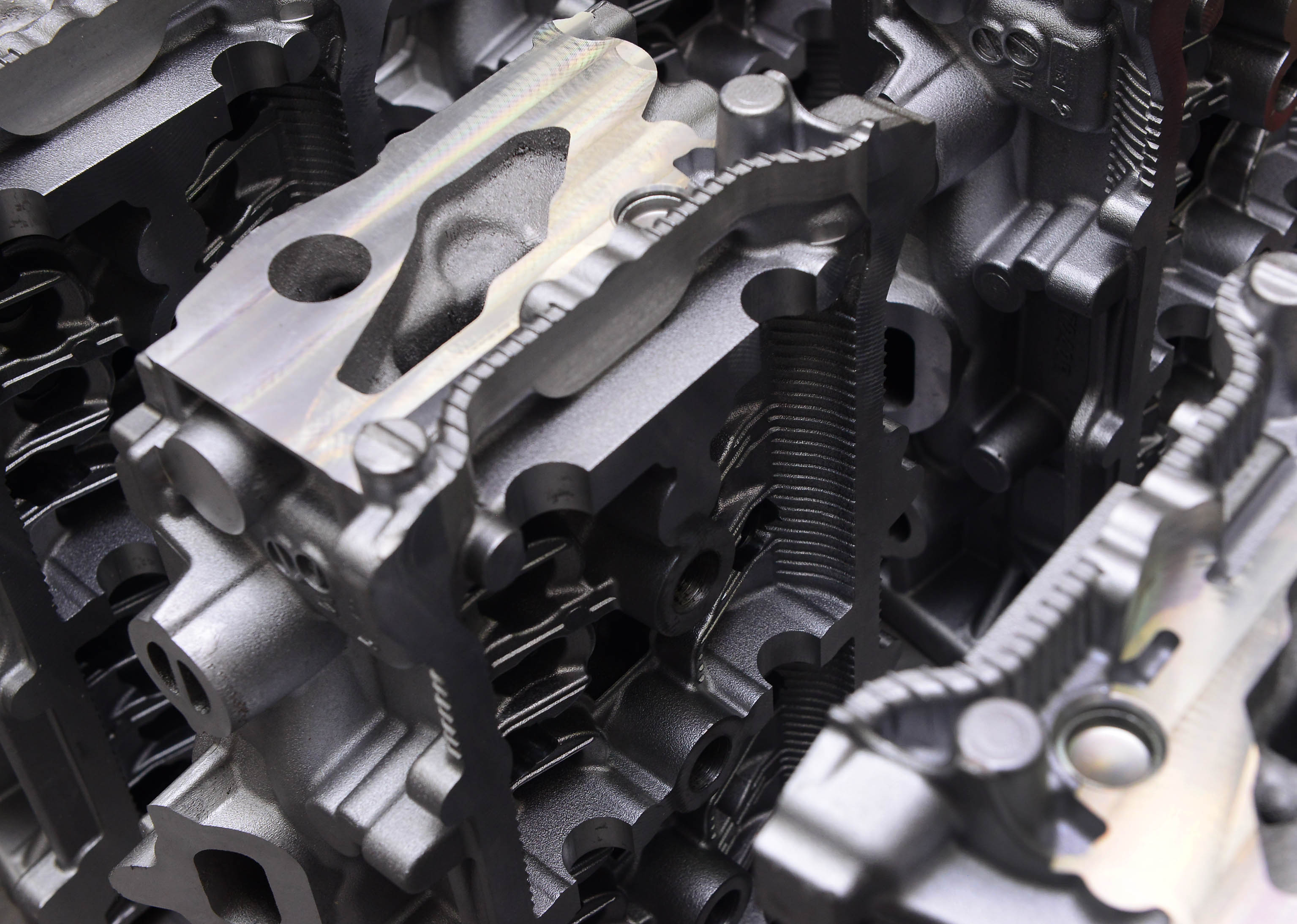
Experience Innovative Reverse Engineering Techniques For Your Project With Us. Our Managed Gateways Ensure A Seamless And Precise Transfer Of Information Throughout The Casting Development And Manufacturing Process. Our System Is Designed To Adhere To The Highest Engineering Standards, Meeting The Diverse Demands Of Our Valued Customers.
In the past, traditional approaches to casting development was by largely trial and error. This would involve producing a casting gating system by a foundry engineer’s best estimate, then if this failed, a second, third etc version would be produced until a satisfactory casting was achieved. As you can imagine, this method took time, wasted money and resulted in longer lead times and expensive parts.
BETTER, MORE INNOVATIVE APPROACH TO CASTING SIMULATION
We knew we could do better. The decision was taken to introduce casting simulation as an imperative tool to run virtual casting trials on a computer. This removes the need to produce multi-casting trials in the foundry. Information obtained via casting simulation can then be used to refine the casting method before a “real” trial is carried out in the foundry.
The goal of casting simulation is to produce a part “right first time” without the time and expense of multiple founding trials. This is achieved by working in partnership with our customers, and using Magma simulation to develop a robust manufacturing method before the first mould is poured. Various alloys can be trialled in a virtual environment to optimise structure and properties by utilising the ‘Magma Iron’ module for casting and ‘Magma Non-Ferrous’ for aluminium castings.
This data is then used in conjunction with our customer’s requirements to maximise properties in the finished component.
Magma simulation also offers an insight in to the residual stress levels in the as cast condition and after heat treatment. This data can then be used to support customer finite element analysis.
CASTING SIMULATION AND MAGMA PHILOSOPHY: RIGHT FIRST TIME
CASTING SIMULATION AND MAGMA EXPERTISE
We have experience of over 500 simulation projects ranging from high specification motorsport to commercial automotive components in Grey, SG, and Compact Graphite Irons, to various aluminium alloys.
All casting simulation predictions are validated by X-Ray, Computerised Tomography (CT), micro examination, and tensile testing. This results in continuous improvements in the accuracy of virtual results obtained by the Magma simulation.
We have extensive experience in the following casting simulation areas:
-
Magma Iron – Structure and properties predictions for iron castings.
-
Magma Non-Ferrous – Structure and properties predictions for aluminium castings.
-
Magma Stress – Residual Stress predictions in the as cast condition.
-
Magma Heat Treatment Stress – Residual Stress prediction during and after heat treatment.
-
Magma Rollover – to support the casting produced using the roll over (Cosworth) process.
-
Magma Link – To support mechanical properties data export to third party analysis systems such as Abaqus, Ansys etc.
We’re one of the few foundries to manage tool making completely in house, in our secure and confidential facility. The origins of our business are in the manufacture of patterns and tooling, and with over 60 years of heritage and experience we have an enviable reputation for technical excellence, quality and service.
Both our pattern making facility and design capability is continually expanding to support our customers demand for directly milled high quality resin patterns and tooling up to fully automated production core-box rigs.
BLENDING THE LATEST TECHNOLOGY WITH UNRIVALED EXPERIENCE
Dedicated CAD resource allows us the ability to work directly with raw data in native formats from Catia, UG and Pro E. Casting accuracy is directly influenced in this phase by the use of high quality materials, trained and experienced staff. The blend of the latest computer aided design technology and unrivalled experience by us provides the highest quality tooling and DFM (Design for Manufacture) experience in support of our customer needs.
BESPOKE TOOLING TO RECONSTRUCT, REPLACE OR REVERSE ENGINEER
In the event of the requirement to reconstruct or replace tooling for a customers discontinued product we are able to reverse engineer from an existing part using the in house tools at our disposal such as Computer Tomography and Optical Scanning. New tooling could then be designed or alternatively printed through our tool less HHS Sand Printer. Moulds can then be constructed re-manufacture a duplicate of the original damaged component.
Our tooling design team will accommodate for the core expansions, gas evolutions and contractions that the mould will experience during the pouring and freezing stages of the casting process.
Our foundry process consultancy was created to bring together the skills in the manufacture of tooling and casting prototypes. This, combined with knowledge and expertise of simulation techniques, project management, product launch and manufacturing process development offers customers a complete ‘design to production’ solution.
OUR EXPERTS WILL HELP YOU THROUGHOUT YOUR PROJECT LIFETIME
We’ve worked together with the world’s leading design consultancies taking concept designs through to mature production. Advanced in house modelling of metal flow and solidification at the prototype phase provides our experts with the key information to permit optimised tooling design, casting methods and subsequently transfer this knowledge through to large scale production runs.
ENGINEERING SERVICES
Foundry process design, the optimisation of foundry tooling and process simulation are central to our engineering service offering.
CASTING EXPERTISE
The Grainger & Worrall casting expertise leads the world in high integrity complex sand castings, supplying automotive OEM’s, Tier 1 suppliers and blue-chip aerospace customers.

FOUNDRY DESIGN
We’ve designed and commissioned multiple new foundries worldwide, our engineers have decades of experience in their field.
Our foundry design consultancy has worked with European, North and South American and Asian operations. Activities include die-casting design methodology for passenger cars, medium and heavy duty diesel engines, racing, performance components and unconventional engine technology.
We can also support you in:
-
Computational analysis of cast components and manufacturing processes such as metal flow and solidification
-
Microstructure
-
Mechanical properties and residual stress
-
Core blowing and gassing.
-
All aspects of process optimisation for metal casting such as metallurgy, running and feeding systems, core and mould making, mould assembly and handling, metal melting and handling, casting finishing operations.
To manage the dynamic of an ever changing marketplace we’ve built and continue to develop a bespoke project management system that successfully supports any size or complexity of project.
A SMOOTH AND ACCURATE TRANSFER OF INFORMATION
Employing a series of managed gate-ways, delivering a smooth and accurate transfer of information throughout the process of casting development and manufacture. The system controls process to provide absolute adherence to the engineering standards demanded by our diverse customer base.
EXPERTISE, EXPERIENCE AND PRECISION
The engineers at Grainger & Worrall that manage customer projects within this system have been drawn from all fields of cast product development and manufacture. These engineers with decades of experience in pattern, tooling manufacture work closely with experts in foundry practice and machining specialists to ensure that the risks associated with any new product are understood from the outset and managed throughout the program through direct integration or support to customer engineering teams as demanded.

NEW PRODUCT INTRODUCTION –
PROCESS MANAGEMENT
Grainger & Worrall have developed a comprehensive process to manage program risk and deliver projects on time and on budget.
We would be pleased to discuss the detail of our approach with you but be assured this robust NPI process is at the heart of our quality offering, combined with a diverse, stable business platform and the provision of accessible managed resources.
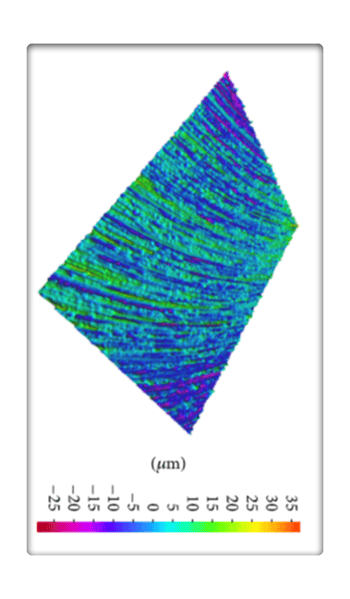
MATERIAL ANALYSIS SPECTROMETERS
All castings produced at Grainger & Worrall are accompanied by full traceability of process variables. Chemical and compositional analysis of sand and metals are made using our laser spectrometry equipment.
This spectral analysis of the melt is undertaken throughout the production process ensuring that the chemical composition of the cast material is correct, results from this activity form the basis of the physical, mechanical and chemical analysis of your product in order that you can be certain of the ultimate mechanical properties of the finished design.
COMPUTER TOMOGRAPHY SYSTEMS | YXLON INDUSTRIAL X-RAY
Computer Tomography is used by Grainger& Worrall in the validation and assurance of casting integrity to create a three dimensional model of the cast component which is then aligned to the customer CAD data.
A surface comparison of the casting enables deviation analysis. CT (Computer Tomography) Scanning also provides a very detailed set of x-ray data for initial material integrity analysis.
The CT department utilises two Yxlon Industrial X-ray machines 24hours a day ensuring integrity of your complex cast aluminium components.
The equipment can be used to scan a wide range of materials and depths. For example:
-
Aluminium up to 250mm
-
Iron up to 80mm
-
Plastic more than 250mm
-
Wood more than 250mm
-
Carbon fibre more than 250mm
-
Silica sand cores more than 250mm
The dimension in (mm) refers to the maximum thickness of material the x-rays are required to penetrate in the horizontal direction.
Grainger & Worrall are able to reverse engineer through the application of this technology, taking a physical part that may no longer have serviceable tooling. Through the production of an integral solid model we can either produce a rapid prototype or new conventional tooling in support of the production replacement parts.
Having invested close to £1Million in multiple CT machines Grainger &Worrall remains the only UK producer of castings with this technology. Over and above other techniques such as Film or Digital Radiography, Computer Tomography provides accurate 3D measurement to within 0.2mm either in visualisation of defects or verification of dimension. For example, the bubbles so damaging to fatigue life due to their oxide- forming movement through the solidifying metal can now be detected with unparalleled accuracy. Even incipient cracks and internal surface imperfections are measurable in a non-destructive way giving certainty to the assessment of quality. Far from relying upon CT to inspect quality. The transparency that CT provides drives the need for continuous design and process improvement.
DIGITAL RADIOGRAPHY
Digital Radiography provides high definition non-destructive testing of casting integrity. Additional processing is also provided including Ultrasonic, Dye penetrant and MPI techniques providing a comprehensive array of testing regimes.
GOM OPTICAL SCANNING
Geometric Optical Measurement at Grainger & Worrall uses a series of white light scans to map the external profiles which are then arranged to produce a 3 Dimensional CAD model. For internal profiles a casting must be sectioned with the internal section scans then being overlaid on the external profile scan to produce a complete model. Fe castings must be sectioned for internal profiles as CT scanning will not work due to the density of the iron
The scanned images of the casting are then converted into a solid model for compatibility with CAD/CAM.
The process of converting a raw data file into solid model file is called Polygonisation. Polygons are used in computer graphics to produce images that are three-dimensional in appearance and are a large series of flat joined surfaces. Once converted the file size will be reduced into a manageable amount and allow the model to be modified for future design use.
The now polygonised model represents the rough As-Cast scanned part.
The surface of the model must therefore be redrawn as a smooth surfaced model for ease of casting and verification of dimensional accuracy.
Surface pickup points are placed on the model profile and used to redraw smooth, continuous surfaces and radii. The new surfaces are joined to create a new 3-D model compatible with CAM software.

CO-ORDINATE MEASURING MACHINES CMM
In house optical Laser scanning and computerised Tomography provides G&W fast and accurate measurement of castings.
Complimenting these computer based technologies CMM and traditional hard line scribing is undertaken when required.
LEAK TESTING
Casting integrity is also checked using either our air decay or water test equipment and is defined in the technical agreement
The challenge of testing a diverse range of castings is the job of our validation team the size of the component and surface finish are duly considered in order the most appropriate method is employed. Many leak testing applications utilise automated plant due to high volumes however in the prototype environment this luxury is not a relevant consideration.
Castings are tested to customer requirements using bespoke test fixturing and are tested according to various specifications which have become much tighter in recent years. These are directly dependent on the fluid the casting is designed to contain or even if vacuum capability is a requirement.
Engine cylinder blocks are often the most challenging type of casting to leak test because they have multiple galleries for oil, coolant and air. Each gallery will often have different leak rates and test pressure.
A variety of leak testing methods can be used, including helium, air, mass flow and pressure decay.


TENSILE TESTING
Tensile testing is undertaken by Grainger & Worrall to validate and determine the yield strength, yield point, tensile strength, elongation, and reduction of area for a given sample.
These tension tests determine the strength and ductility of the cast materials under uniaxial tensile stresses. The results are helpful in comparisons of materials, in the development of new alloys, for quality control.
Proper test piece alignment, grip and face selection are critical factors in obtaining valid test results. Bending moments or side loading are avoided, we custom design and manufacture fixtures to provide repeatable results.
PROCESS QUALITY SYSTEM
Grainger & Worrall supply product and expertise across the world. The markets served are as diverse as Formula 1, aerospace through to construction and defence projects.
Our challenge has been to provide our customers with quality systems and tools which are tailored to their environments.
The main stay of the process is a project management system which engenders team and individual responsibility with the objective of delivering excellence in our products, processes and timing.

A SMOOTH AND ACCURATE TRANSFER OF INFORMATION
Employing a series of managed gate-ways, delivering a smooth and accurate transfer of information throughout the process of casting development and manufacture. The system controls process to provide absolute adherence to the engineering standards demanded by our diverse customer base.
ACCURACY, KNOWLEDGE AND CASTING SKILL
Our team of engineers draws from a wide range of cast product development and manufacturing backgrounds. With decades of experience in pattern and tooling manufacturing, we work alongside foundry and machining experts to identify and manage any potential project risks. This team ensures that projects are managed efficiently and effectively, from inception to completion.
