Advanced CNC and Precision Machining Solutions.
We specialise in complex prismatic precision machining worldwide.
Machining at Grainger and Worrall
State-of-the-art, fully air-conditioned 3,000m2 facility. Modern high-spec machining centres, metrology lab, engineers and programmers.

Why Choose Us?
We are Grainger & Worrall Machining (GWM). We provide integrated machining services for castings produced in-house as well as serving third parties with specialist machining for machined-only parts from casting or billet.
We use High-Spec CNC machining centres (3-axis to 5-axis) with up to 24 station Flexible Manufacturing Systems (FMS). Everything is specified to use the best available – from Coordinate Measurement Machines, CNC programming software and tooling right down to the latest in coolant technology and electronic part-level marking and traceability.
The facility is used for machining, measuring and finishing a wide range of high-complexity prismatic parts, including engine blocks, cylinder heads, battery trays, electric drive units, structural parts, gearbox housings and a wide variety of specialist components.
Our 3,000 m2 facility is fully air-conditioned. This not only provides a great environment for our highly skilled workforce but also removes variables from the process and means that our machines are always operating in an optimal environment. The constant temperature gives us an advantage when it comes to ultimate dimensional accuracy, but it also allows us to take in process measurements for process control without having to contend with inaccuracies that would be caused by temperature variation.
Our facility is specified, built, and maintained to meet stringent market demands. We invite you to see it for yourself. Contact us to book a tour or a free project review.
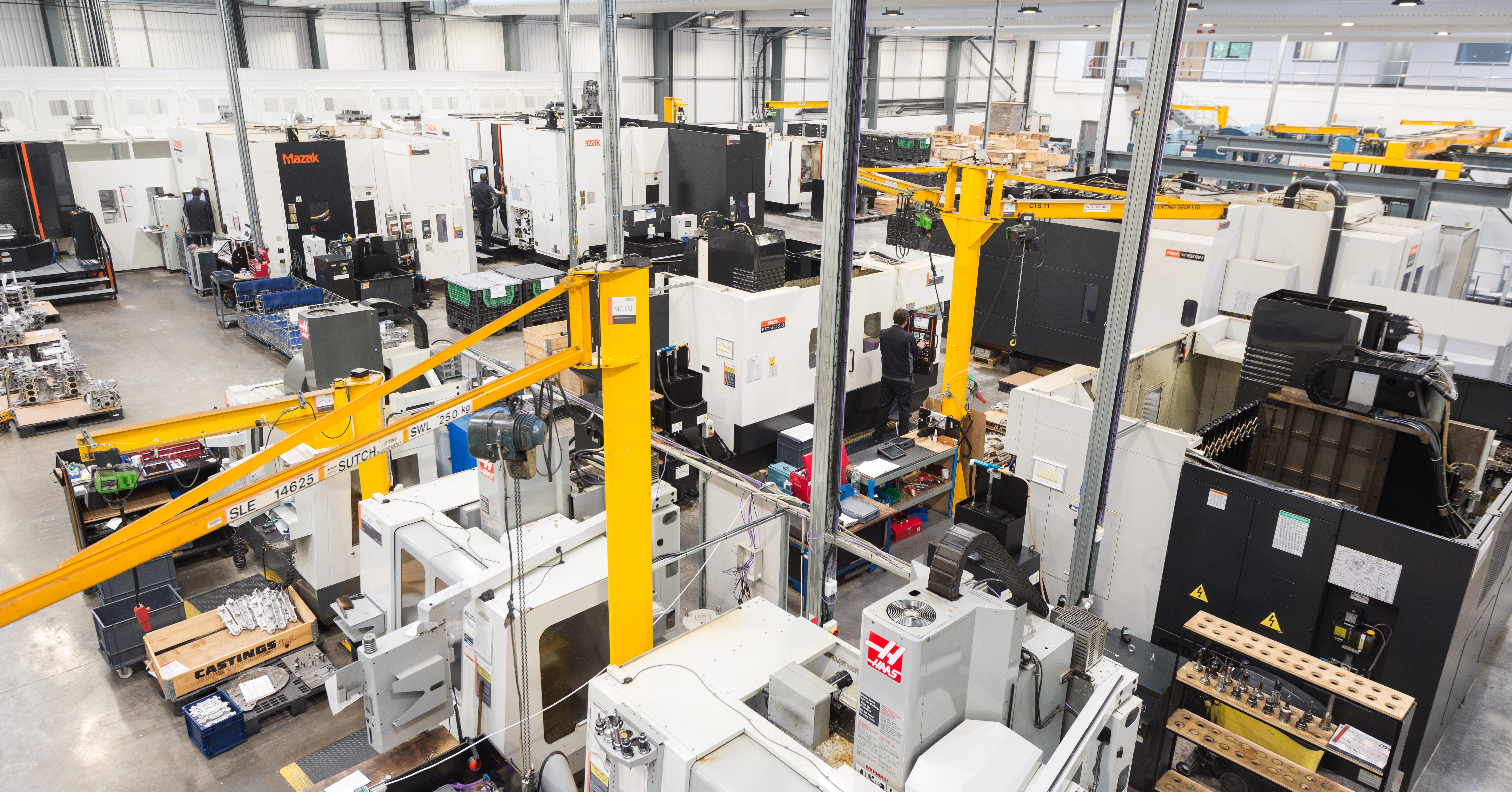
At Grainger & Worrall, we specialise in the precision machining of high-complexity aluminium alloy castings, serving a diverse range of sectors including automotive, motorsport, aerospace, defence, marine, and architectural industries.
Utilising advanced CNC technology, including 5-axis machining centres, we ensure high levels of accuracy and efficiency. This capability allows us to meet the stringent requirements of various industries, delivering components with exceptional precision and quality.
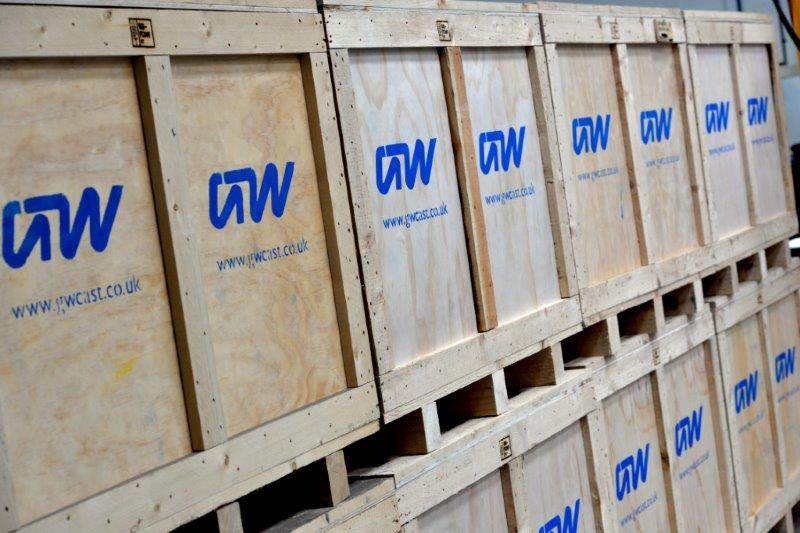
Our flexible manufacturing system is designed to accommodate rapid prototyping and small-batch production, enabling quick turnaround times and the ability to make frequent modifications as needed. Our continuous investment in cutting-edge technology and skilled personnel ensures that we remain at the forefront of the industry, providing innovative solutions tailored to the unique needs of each sector we serve.
Quality Assured Precision Machining Capabilities
CNC machining services with assured quality and precision for your project.
When it comes to machining, you need the entire production process to be quality-assured, precise and reliable. This integrity is why we’ve invested heavily in our quality assurance processes to ensure we have robust, accurate quality checks in place. No matter at what point in the process, you’ll have complete confidence in the outcome.
Your high standards are our high standards.
WANT ACCURATE INSPECTION CHECKS THROUGHOUT THE MACHINING PROCESS?
That’s no problem. To support your exacting specifications, we’ve invested heavily in the latest CMM hardware & software.
-
We use the latest PC-DMIS software to guarantee we can quickly and accurately inspect any feature which we’ve machined.
-
Our multiple DEA CMM machines mean that producing inspection reports in an internationally recognised format is easy, referencing back to your original drawing.
If you need in-process critical feature checks, SPC or capability studies, they’re no problem either. Our CMM machines collect and process data reliably to meet your specifications.
If required, many machined features can be checked before they even leave the machine table with:
-
air gauging
-
hard gauging
-
more specific hand-held inspection devices.
It goes without saying that this is all traceable at serial number level for individual part identification.
Put simply, we want to make your life easier. That's why we offer comprehensive procurement outsourcing in support of our precision machining services. This second-tier supplier management and quality-guaranteed machining service is designed to allow you to focus on the overall product, as well as reduce product development support costs.
Invaluable Procurement Support for Your Entire Project
Whether you have an integrated procurement team or not, we can manage subcontracted service providers for you, using our valuable experience to support you across your whole project. Our machining support services include:
-
Technical liaison and DFM support
-
SQA
-
Contract management
-
Cost reduction
-
Progress chasing
This is invaluable, as the project team is developed by the customer to support the actual production procurement activities in the longer term of the project.
